Welding with a welding data management system
You work with a welding data management system to automatically record the actual welding parameters per weld, per product and per project. In this way, you quickly and efficiently build a report for your client.
Digitalization of welding
The future of welding lies in paperless work or digitization. Sooner or later every company will have to deal with this. CNC machines, robots and microprocessor controlled welding machines improve both the production processes and the quality of the goods produced. By properly analyzing all process data you can improve and speed up the production process giving you an advantage over your competition.
Quality assurance and traceability
Can you guarantee your customers that welding is done in accordance with the guidelines? With the help of the welding data you can really prove the quality. You can prove at any time that the production was carried out with the required parameters. So there is no reason for discussion afterwards.
Quality assurance and traceability
Can you guarantee your customers that welding is done in accordance with the guidelines? With the help of the welding data you can really prove the quality. You can prove at any time that the production was carried out with the required parameters. So there is no reason for discussion afterwards.
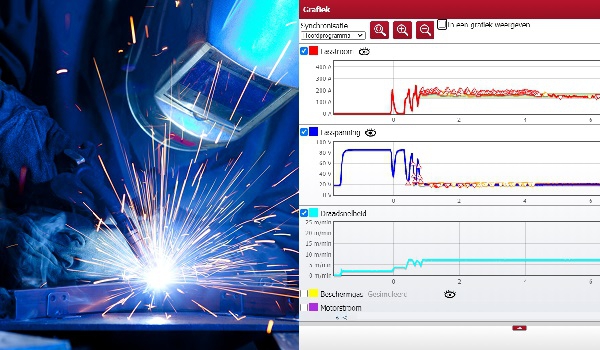
What you can do with a welding data management system
Elektrolas believes in the welding management system Xnet, from the high-quality German welding machine manufacturer EWM. This software system consists of:
- Registration of welding data
- Central storage, viewing and analysis
- Online monitoring - control and monitoring of welding processes on a desired number of welding machines
- Analysis, evaluation, reporting and documentation of welding parameters recorded online
- Transfer possibility to all welding machines on the network
- Convenient and easy to set up graphic layout of all network users
EWM Xnet has different modules like the starter kit, WPQ-X Manager and component management. With these modules you can continuously record and document welding parameters to ensure quality. The additional valuation of this data can provide measures for more efficient production. Furthermore, you can create and manage welding method descriptions (WPS) and assign welders. You can also manage components, set up welding sequences and assign welding instructions.
Connecting welding machines
The new welding machines are equipped with microprocessors that are open for data exchange. Multiple welding machines can be connected to each other. In addition, the installation of the welding data management system is necessary. This requires a server and a LAN or WIFI connection. During the welding process the different welding data are directly stored on the server. This way they can be analyzed and evaluated during the welding process but also afterwards. Offiline is also possible. Then the welding data is stored and documented on a USB stick.
Maintenance at the right time
To extend the life of a welding machine and to keep the quality high, maintenance on the machines is necessary. The optimal time for maintenance and repair work can be determined by means of the retrieved data. That is when a component really needs to be replaced because it no longer functions.
What will your future be?
Are you ready for it? As far as Elektrolas is concerned, one thing is certain. Elektrolas is working on the solution that fits you production of tomorrow. Innovate together. Contact us via phone: 0416-336777 or mail info@elektrolas.com. Or leave your information.
Our overall approach
When it comes to welding, Elektrolas has all the knowledge and resources in-house. We are a point of contact for all those involved in the welding process, from tendering to quality control. We are a total provider in the welding field. We secure quality, offer training, sell, rent and service on welding equipment. This is our disc-of-five. Five services that reinforce each other. That is how we ensure that our customers are ready for the future.
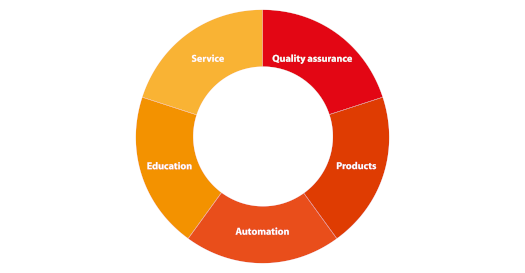